Fatto a mano
In Gregario coltiviamo da sempre stima e rispetto per la tradizione telaistica artigiana del nostro bel Paese, quella che si dedica ad una nicchia di prodotto “classico” intramontabile, con l’acciaio in primis, ma anche con il carbonio fasciato e altre tecniche tipiche dell’atelier.
Dunque lunga vita agli artigiani telaisti e a chiunque si dedichi a preservare e tramandare una ars technica nobile e affascinante!
Ciò premesso, ci è capitato di incrociare recentemente alcuni post social di diversi stimati artigiani della bicicletta che esaltando le (indubbie) qualità dei propri telai mettono il loro “fatto a mano” in contrapposizione ai telai “stampati” in carbonio monoscocca. Detta così sembra una rivendicazione più che legittima, ma questa narrazione induce una disinformazione importante su COME vengono effettivamente prodotti i telai “stampati”… vale a dire con un lavoro manuale decisamente più impegnativo e oneroso di qualsiasi tecnica di giunzione degli otto tubi.
Eh già, perchè non stiamo parlando di stampare biscotti, bensì di disporre accuratamente oltre 200 sagome di tessuto (carbonio preimpregnato) all’interno di uno stampo. Parliamo di ritagli che vanno dalla pezza “lunga” 40 cm a francobolli di pochi cm, che devono essere posizionati a mano secondo uno schema preciso (il cosiddetto ply-book), con sovrapposizioni accurate, risvolti da gestire e direzioni della fibra da rispettare. E questa è soltanto una buona metà del lavoro, perché poi, a seconda della tecnologia di cura della resina utilizzata, ci sono una serie di ulteriori operazioni da fare, sempre rigorosamente a mano.
Nel caso dell’autoclave (tecnica più diffusa in Europa) è necessario disporre con estrema cura i sacchi interni, chiudere i due semistampi senza “pizzicare” nulla, disporre una serie di materiali ausiliari, chiudere il sacco esterno, applicare il mastice per collegare i sacchi interni con l’esterno e così via fino al momento in cui tutto viene mandato a temperatura e pressione. Inoltre, finita la “cottura”, si procede, ancora una volta a mano, con l’apertura dello stampo, l’estrazione del pezzo e fasi di finitura. Tutto ciò con una serie di possibili varianti operative in cui non ci addentriamo.
Dunque non c’è niente che sia più “fatto a mano” di un telaio monoscocca in carbonio.
E allora le produzioni (spesso asiatiche) in serie?
La distinzione tra artigianale e industriale non sta certo nel materiale o nella tecnica specifica, ma nell’organizzazione del lavoro. Qualunque tecnica può essere analizzata, semplificata, scomposta e organizzata in modo industriale per tentare di renderla economica (e quindi profittevole) su grande scala. Che si tratti di mettere in piedi linee di saldatura semi-automatica o catene di laminatori in cui ciascuno è dedicato a disporre ripetutamente le stesse 3 pezze di carbonio per l’intera giornata, il fine è sempre uno: produrre tanti pezzi a basso costo. Vale in qualsiasi ambito: esiste l’intagliatore artigiano che produce pezzi unici in legno ed esistono manufatti seriali intagliati con macchinari evoluti per il mercato di massa.
E’ qui che si gioca la vera scelta del cliente finale: prodotto seriale o prodotto unico?
Sceglierà il lavoro di molte mani in catena di produzione o di pochi individui appassionati?
Certo è una scelta che non tutti si possono permettere e da questo punto di vista la serialità in sé non è neanche un male se permette di abbattere il prezzo finale rendendo più accessibile un prodotto sul mercato. Tuttavia i produttori “seriali” non si accontentano del basso e medio di gamma, ma vogliono sempre più quote di mercato anche nell’alta gamma e nel lusso cercando di vendere l’unicità dove non esiste per giustificare prezzi “da alto artigianato” anche su prodotti di massa e avere margini da capogiro. Vendono l’illusione dell’unicità e trovano clienti disposti a comprarla.
Gregario è un laboratorio “ibrido” in cui l’artigianalità si coniuga con ingegneria, tecnologia e innovazione, sviluppando processi originali alla ricerca di nuovi sentieri da esplorare: una telaistica su misura evoluta (monoscocca integrale), che prosegue la tradizione del “fatto a mano” senza rinunciare alle tante innovazioni che caratterizzano la moderna bicicletta di alta gamma. Le tecnologie ed i processi che sviluppiamo nascono dall’ambizione di perseguire ostinatamente la perfezione personalizzando “a misura” del singolo ciclista ciò che fino ad oggi era accessibile solo in taglie standard ovvero il monoscocca integrale con tutti i suoi pregi: libertà di forme e design e quindi aerodinamica oltre ad una piena espressione del potenziale della fibra, che strutturalmente lavora bene se ha continuità, senza fasciature, incollaggi o altre tecniche di giunzione.
Oggi Gregario preferisce dedicare risorse ed energie nel perseguire l’unicità e la bellezza anche a scapito di maggiori costi di produzione, nella certezza che con il tempo le tecnologie sviluppate dal nostro laboratorio potranno essere scalate e rese accessibili ad una platea più ampia di appassionati.
Invece di sgomitare tra piccoli produttori di pezzi “unici” dovremmo guardarci negli occhi e riconoscerci tra simili, persone a cui piace costruire il valore dell’unicità dedicando tempo ad ogni singolo prodotto del nostro lavoro e non alla sua serializzazione.
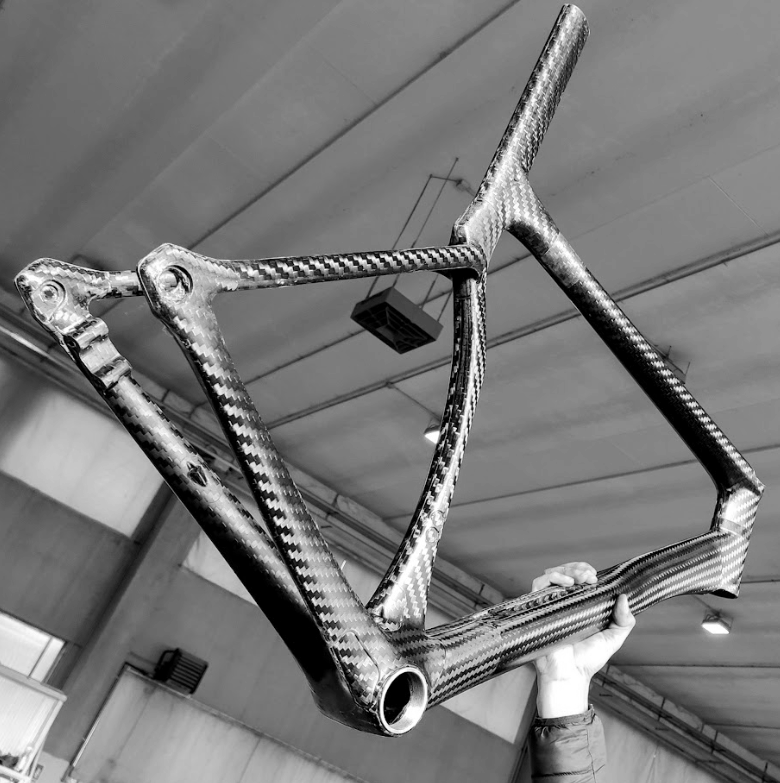